We provide custom solutions to all our customers and offer complete technical advices that your company can take advantage of.
The design and materials of the extrusion screw play a crucial role in the performance of the extrusion process.
The design and materials of the screw can vary depending on the specific application and the properties of the material that is being extruded.
The manufacturing process of extrusion screws typically includes the steps of design and engineering, material selection, machining, surface treatment, inspection and testing, and final packaging and shipping.
It's important to choose the right screw design and dimension, as well as the appropriate pitch and materials, to ensure the best performance in the extrusion process.
I. Introduction
A. Definition of extrusion screw
B. Purpose of extrusion screw
C. Overview of the different types of extrusion screws
II. Design and Materials
A. Single screw vs twin screw extrusion
B. Dimension and pitch of the screw
C. Depth of the screw
D. Materials used in the manufacturing process
A. Plastics manufacturing
B. Food processing
C. Other industries that use extrusion screws
A. Design and engineering
B. Material selection
C. Machining
D. Surface treatment
E. Inspection and testing
Definition of extrusion screw
An extrusion screw is a device that is used to move and shape a material, typically a plastic or a food product, through a process called extrusion. The screw is typically made of metal and is placed inside a barrel, which is also known as an extruder. The screw is powered by a motor and rotates, pushing the material forward through the barrel. The shape of the screw can vary depending on the type of extrusion process and the material being extruded. The screw can have a single flight or multiple flights, and its design can affect the flow rate, pressure, and temperature of the material as it is pushed through the barrel.
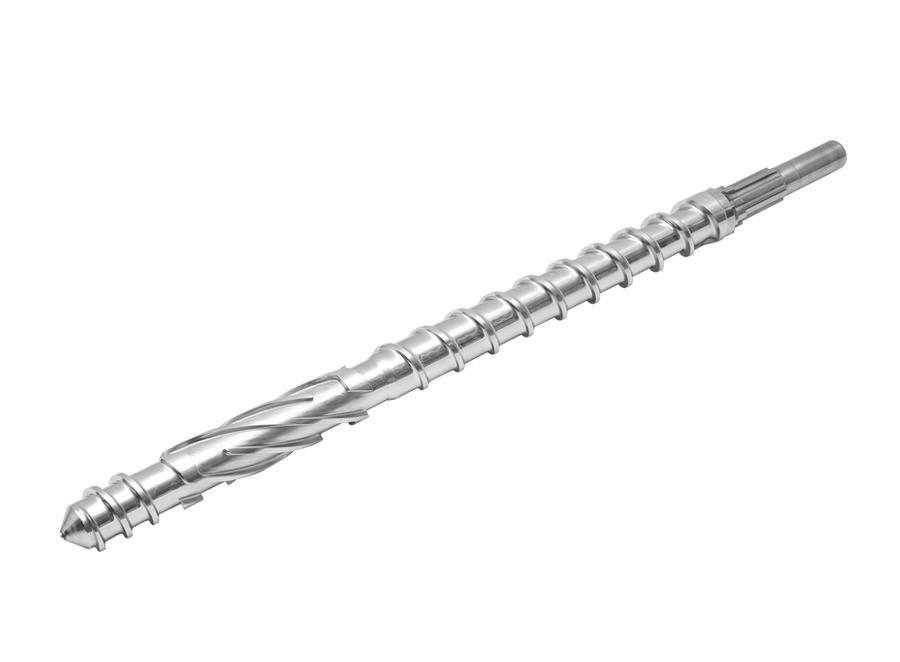
Purpose of extrusion screw
The purpose of an extrusion screw is to move and shape the material that is being extruded through the barrel of the extruder. The screw is designed to exert a force on the material, pushing it forward and through a die at the end of the barrel. The design of the screw can also be used to control the pressure, temperature, and flow rate of the material as it is extruded. Additionally, the screw can be used to mix, homogenize, or heat the material as it is extruded. The extrusion screw is an essential component in the extrusion process, which is used in a wide range of industrial applications, such as manufacturing plastic products, food products, and pharmaceutical products.
Overview of the different types of extrusion screws
There are several different types of extrusion screws, each with their own unique design and purpose. Some of the most common types of extrusion screws include:
Single screw extrusion: As the name suggests, this type of extrusion screw has a single flight, or helix, and is typically used for simple extrusion processes where the material is pushed through a die to achieve a specific shape.
Twin screw extrusion: This type of extrusion screw has two parallel screws that rotate in opposite directions. It is used for more complex extrusion processes where the material needs to be mixed, heated, or homogenized as it is extruded.
Screws with barrier flights: This type of screw is designed to create a barrier between the feed material and the metered material, which allows for better control of the extrusion process.
Screws with mixing elements: This type of screw is designed with elements that help to mix the material as it is extruded, which is particularly useful for materials that have a tendency to separate or settle during the extrusion process.
Screws with pin elements : This type of screw is designed with pin elements, which increase the specific surface area of the material and promote better heat transfer, which is particularly useful for materials that are difficult to heat.
Screws with grooved flights : This type of screw is designed with grooves on the flight, which increase the specific surface area of the material and promote better heat transfer, which is particularly useful for materials that are difficult to heat.
It's important to note that the type of extrusion screw used depends on the specific application and the properties of the material that is being extruded.
Single screw vs twin screw extrusion
Single screw extrusion and twin screw extrusion are two different types of extrusion processes that are commonly used in various industries.
Single screw extrusion uses a single screw that rotates within a barrel, pushing the material through a die to achieve the desired shape. This type of extrusion is simple and straightforward, and is typically used for materials that are easy to process and do not require much modification during the extrusion process. Single screw extrusion is commonly used to produce products such as pipes, sheets, and simple profiles.
Twin screw extrusion, on the other hand, uses two parallel screws that rotate in opposite directions. This type of extrusion is more complex and allows for better control of the extrusion process. The twin screws can be used to mix, heat, or homogenize the material as it is extruded. This type of extrusion is commonly used for materials that are difficult to process or that require modification during the extrusion process. Twin screw extrusion is used to produce products such as pellets, fibers, and complex profiles.
It's important to note that each type of extrusion process has its own advantages and disadvantages, and the choice of which one to use depends on the specific application and the properties of the material that is being extruded.
Dimension and pitch of the screw
The dimensions and pitch of an extrusion screw are important factors that affect the performance of the extrusion process.
The dimensions of the screw include the diameter and the length of the screw. The diameter of the screw is typically chosen based on the size of the barrel and the material being extruded. The length of the screw is determined by the amount of material that needs to be extruded and the desired output rate.
The pitch of the screw refers to the distance between the flights or helixes of the screw. The pitch can be either constant or variable, and it affects the flow rate of the material as it is extruded. A screw with a larger pitch will have a higher flow rate, while a screw with a smaller pitch will have a lower flow rate. The pitch also affects the pressure that the screw exerts on the material, with a larger pitch resulting in a higher pressure.
The combination of the dimension and pitch of the screw, along with the screw's design, plays a crucial role in the output rate, the pressure, and the temperature of the extruded material. It's important to choose the right screw design and dimension, as well as the appropriate pitch, to ensure the best performance in the extrusion process.
Depth of the screw
The depth of the screw refers to the distance between the tip of the screw and the root of the screw flights. This dimension is also known as the "screw channel depth" or "screw root depth". It's an important factor that affects the performance of the extrusion process.
A deeper screw channel allows for a greater volume of material to be held within the screw, which can increase the output rate of the extruder. However, a deeper screw channel can also increase the pressure inside the barrel, which can lead to higher energy consumption and higher extruder temperatures.
A shallower screw channel, on the other hand, can reduce the pressure inside the barrel and lower the energy consumption, but it can also decrease the output rate of the extruder.
The depth of the screw also affects the heat transfer between the screw and the material. A deeper screw channel can reduce the heat transfer between the screw and the material, which can lead to higher extruder temperatures. A shallower screw channel, on the other hand, can increase the heat transfer between the screw and the material, which can lower the extruder temperatures.
In summary, the depth of the screw is a balance between the output rate and the energy consumption, the balance should be achieved taking into account the properties of the material and the desired final product.
Materials used in the manufacturing process
The materials used in the manufacturing process of extrusion screws can vary depending on the specific application and the properties of the material that is being extruded. The most common materials used to make extrusion screws include:
Steel: Steel is a strong and durable material that is commonly used to make extrusion screws. It can withstand high temperatures and pressures, and is resistant to wear and tear.
Stainless steel: Stainless steel is a corrosion-resistant material that is commonly used to make extrusion screws for food processing applications.
Hardened steel: Hardened steel is a type of steel that has been heat-treated to increase its strength and wear resistance. It is commonly used to make extrusion screws for abrasive or high-wear applications.
Tool steel: Tool steel is a type of steel that is known for its high wear resistance and toughness. It is commonly used to make extrusion screws for high-wear or abrasive applications.
Nickel-based alloys: Nickel-based alloys, such as Inconel and Hastelloy, are known for their high temperature resistance and corrosion resistance. They are commonly used to make extrusion screws for high-temperature or corrosive applications.
Tungsten carbide: Tungsten carbide is a very hard and wear-resistant material that is commonly used to make extrusion screws for abrasive or high-wear applications.
Applications
Plastics manufacturing: Extrusion screws are used in the manufacturing of a wide range of plastic products, such as pipes, sheets, and profiles. The extrusion process is used to melt plastic pellets or granules and shape them into the desired product.
Food processing: Extrusion screws are used in food processing applications to mix, heat, and shape food products. They are commonly used to produce pasta, breakfast cereals, and snack foods.
Pharmaceuticals: Extrusion screws are used to produce tablets and capsules in the pharmaceutical industry. The extrusion process is used to mix, heat, and shape the active ingredients and excipients into a granulate, which is then compressed into tablets or filled into capsules.
Chemicals and fertilizers: Extrusion screws are used to produce a wide range of chemical and fertilizer products. The extrusion process is used to mix, heat, and shape the raw materials into the desired product.
Textile fibers: Extrusion screws are used to produce a wide range of textile fibers. The extrusion process is used to melt and shape the polymer into a fiber, which is then cooled and drawn.
Wood-plastic composites: Extrusion screws are used to produce wood-plastic composites. The extrusion process is used to mix, heat, and shape the wood fibers and plastic into a composite material.
Recycling: Extrusion screws are used to recycle plastic waste, by melting, mixing and shaping it into a new product.
Extrusion Screw Manufacturing Process
Design and engineering: The first step in the manufacturing process is to create a design for the extrusion screw. The design will take into account the specific application, the properties of the material that is being extruded, and the desired final product. Engineers will use specialized software to create a 3D model of the screw, which will be used to guide the manufacturing process.
Material selection: The next step is to select the appropriate material for the screw. The selection will depend on the specific application and the properties of the material that is being extruded. The material selection will also take into account the specific requirements of the final product, such as food contact, corrosion resistance, high temperature resistance among others.
Machining: After the material is selected, the screw is machined to the desired dimensions and shape. This typically involves using CNC machines to cut and shape the screw from a solid piece of metal.
Surface treatment: Once the screw has been machined, it may undergo a surface treatment process. This can include heat treatment, nitriding, hardening, or other processes that are used to improve the wear resistance, corrosion resistance, and overall performance of the screw.
Inspection and testing: Before the screw is shipped to the customer, it is inspected and tested to ensure that it meets the customer's specifications and that it is free of defects. This may include performing a visual inspection, measuring the dimensions, and performing a functional test.
Final packaging and shipping: Once the screw is inspected and tested, it is packaged and shipped to the customer. The package will include a drawing of the screw and a certificate of conformity.
Barrelize extrusion screws are produced to fit your specific application, no matter What OEM Brand. We also offer free extrusion screw calculation for our customers.
Barrelize extrusion screws are produced to fit your specific application, no matter What OEM Brand. We also offer free extrusion screw calculation for our customers.