We provide custom solutions to all our customers and offer complete technical advices that your company can take advantage of.
There are several surface treatment methods that can be used to improve the performance and lifespan of screw and barrel components in plastic processing equipment. Some common methods include:
1. Nitriding: This is a heat treatment process that introduces nitrogen into the surface of the metal, improving its wear resistance and fatigue strength.
Nitriding is often used on steel and other high-strength, low-alloy steels to improve their surface properties.
There are several different methods of nitriding, including gas nitriding, salt bath nitriding, and plasma nitriding. In gas nitriding, the metal component is heated in an atmosphere of ammonia gas, which diffuses nitrogen into the surface of the metal. In salt bath nitriding, the metal component is heated in a molten salt bath, which also introduces nitrogen into the surface of the metal. In plasma nitriding, a plasma flame is used to introduce nitrogen into the surface of the metal.
2. Hard chrome plating: This process involves applying a layer of hard, corrosion-resistant chromium to the surface of the metal.
The process of hard chrome plating involves electroplating a thin layer of chromium onto the surface of the metal using an electric current. The chromium is applied in a solution containing chromic acid, which is then electroplated onto the surface of the metal. The thickness of the chromium layer can be controlled by adjusting the electric current and the duration of the plating process.
3. Tungsten carbide coating: This is a process in which a layer of tungsten carbide is applied to the surface of the metal using a thermal spray process. Tungsten carbide is a very hard, wear-resistant material that can improve the performance of screw and barrel components.
There are several thermal spray processes that can be used to apply tungsten carbide coatings, including plasma spray, high velocity oxy-fuel (HVOF) spray, and detonation gun spray. In these processes, a stream of tungsten carbide particles is sprayed onto the surface of the metal using high temperatures and pressure. The particles bond to the surface of the metal to form a hard, wear-resistant layer.
4. Thermal spray coatings: These coatings, such as aluminum oxide or ceramic, are applied to the surface of the metal using a thermal spray process. They can improve the wear resistance and corrosion resistance of the metal.
There are several different types of thermal spray coatings, including aluminum oxide, ceramic, and tungsten carbide coatings. These coatings can be used to improve the wear resistance, corrosion resistance, and surface finish of metal components. They are often used in industries such as aerospace, automotive, and manufacturing to protect metal parts from wear and corrosion.
5. Polishing: This process involves smoothing and shining the surface of the metal using abrasive materials. Polishing can improve the surface finish and reduce friction between the screw and barrel.
There are several different methods of polishing, including hand polishing, buffing, and tumbling. Hand polishing involves using abrasive materials, such as sandpaper or steel wool, to manually smooth and shine the surface of the metal. Buffing involves using a buffing wheel and abrasive compound to polish the metal. Tumbling involves placing the metal components in a tumbler with abrasive media, such as ceramic or plastic, and tumbling them for a period of time to polish the surface.
Barrelize can operate several treatments in-house such as Nitride, bimetallic, chrome plating, Physical vapor deposition coating, or customized coating.
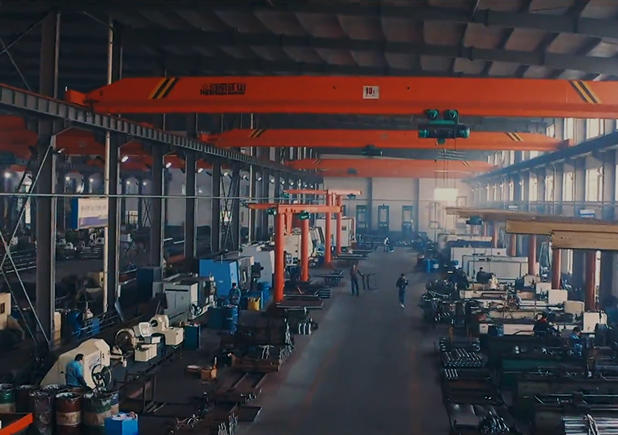