We provide custom solutions to all our customers and offer complete technical advices that your company can take advantage of.
Injection molding is a manufacturing process in which a material, typically plastic, is melted and injected by a machine into a mold. The screw in an injection molding machine helps to both heat and transport the melted material into the mold. The design of the screw is an important factor in the efficiency and quality of the injection molding process.
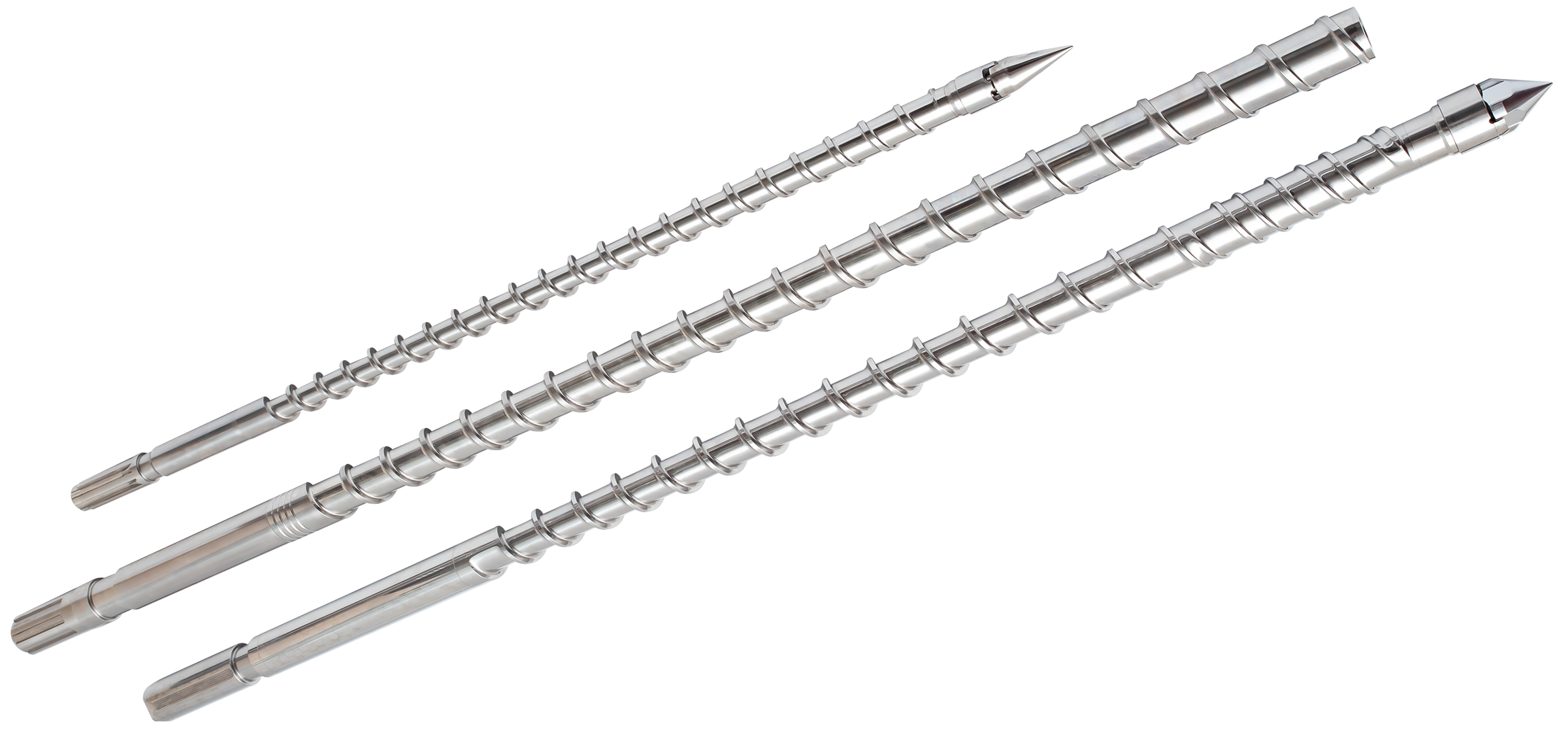
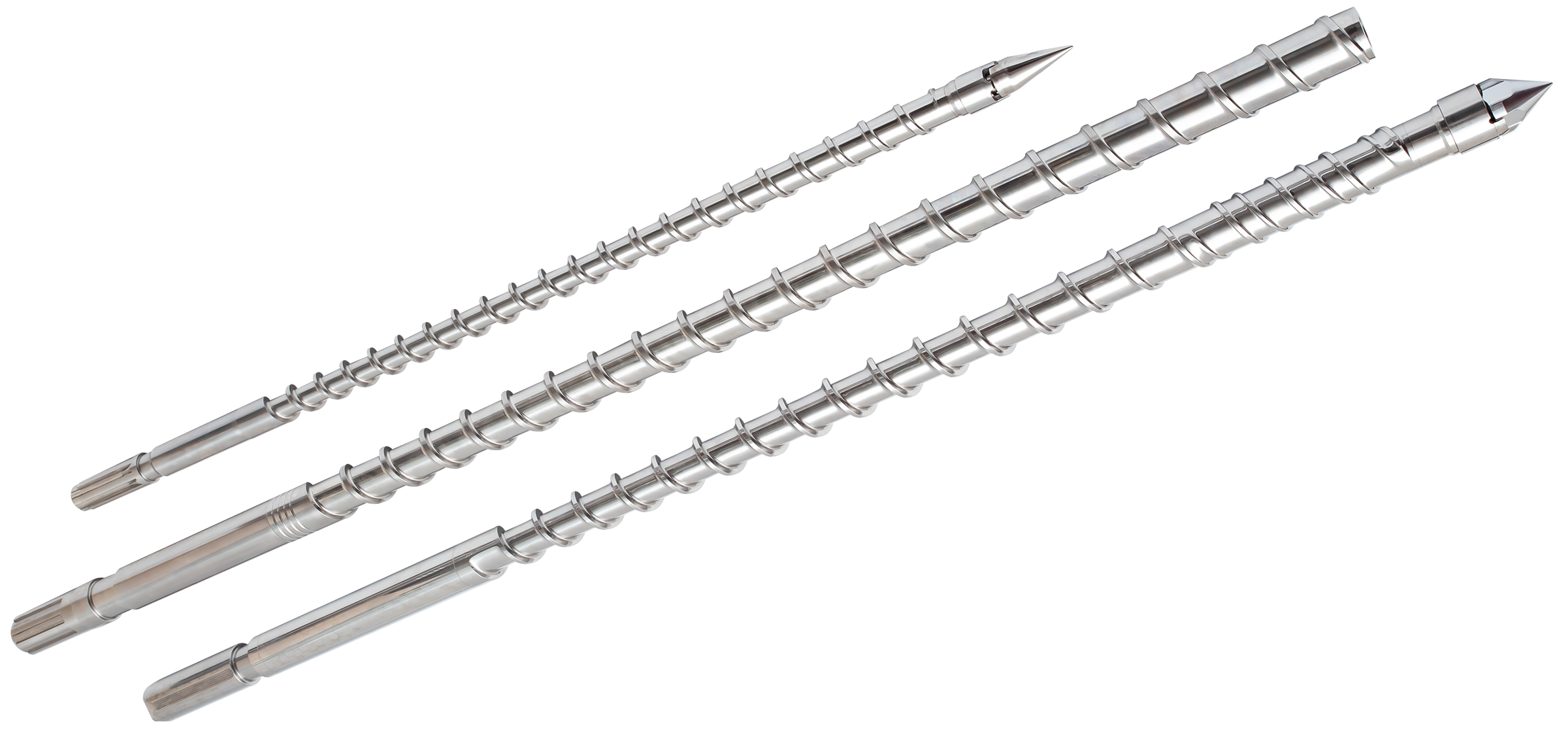
There are several factors to consider when designing an injection molding screw:
1. Material: The type of material being molded will affect the design of the screw. Different materials have different melting temperatures and flow properties, and the screw must be designed to handle these properties effectively.
2. Processing temperature: The processing temperature refers to the temperature at which the material is injected into the mold. The screw must be able to maintain this temperature as it transports the material through the machine.
3. Pressure: The pressure at which the material is injected into the mold will affect the design of the screw. Higher pressure can be used to fill the mold more quickly, but it can also cause the material to degrade or cause other problems if not carefully controlled.
4. Residence time: The residence time refers to the amount of time that the material spends in the barrel of the injection molding machine. The screw must be designed to optimize the residence time to ensure that the material is fully melted and homogenized before it is injected into the mold.
5. Melting and mixing: The screw must be designed to effectively melt and mix the material as it is transported through the barrel of the machine. This is typically achieved through the use of specific screw geometries and flight configurations.
PVC injection molding screw design
PVC (polyvinyl chloride) is a commonly used plastic material in injection molding. It has good strength, rigidity, and weather resistance, and it can be easily molded into a variety of shapes and products.
When designing a screw for PVC injection molding, there are several factors to consider:
1. Melting temperature: PVC has a melting temperature of around 220-270°C, depending on the specific formulation. The screw must be able to maintain this temperature as it transports the material through the machine.
2. Residence time: PVC has a relatively low melting temperature and can degrade if it spends too much time in the barrel of the injection molding machine. The screw must be designed to optimize the residence time to ensure that the material is fully melted and homogenized before it is injected into the mold.
3. Mixing: PVC has a tendency to segregate, or separate, during the injection molding process. The screw must be designed to effectively mix the material as it is transported through the barrel of the machine to ensure a uniform end product.
4. Pressure: PVC has a relatively low melting point, so it is typically injected at lower pressures compared to other materials. The screw must be designed to generate the appropriate level of pressure to fill the mold effectively without causing the material to degrade.
In summary, the design of the injection molding screw is an important factor in the efficiency and quality of the injection molding process. It must be carefully designed to handle the specific properties of the material being molded and to optimize the various process parameters.