We provide custom solutions to all our customers and offer complete technical advices that your company can take advantage of.
Feed screw is a type of screw used to mix solids and liquids. Different materials have different processing requirements. There are two types of mixing: Distributive and dispersive. Distributive mixing involves high shear rates while dispersive mixing involves spreading particles and agglomerates. Each type of mixing is used to varying degrees, and the feed screw needs to take this into account.
GP screw
In the extrusion process, the selection of the correct screw design is critical to optimizing melt conditions and maximizing material properties. The physical properties of plastic materials vary widely and can be sensitive to contamination and shear. The GP feed screw was developed to meet these challenges. Here are a few important things to consider when choosing the correct screw design.
The GP feed screw is a single-flighted compression screw that features three zones: the feed zone, the compression zone, and the metering zone. The pitch and thread width of the screw equal its diameter, and the taper of the compression zone is cut according to an involute pattern. The compression ratio is between 2:1 and 3:1. The screw is used to process a wide variety of resins and shot sizes.
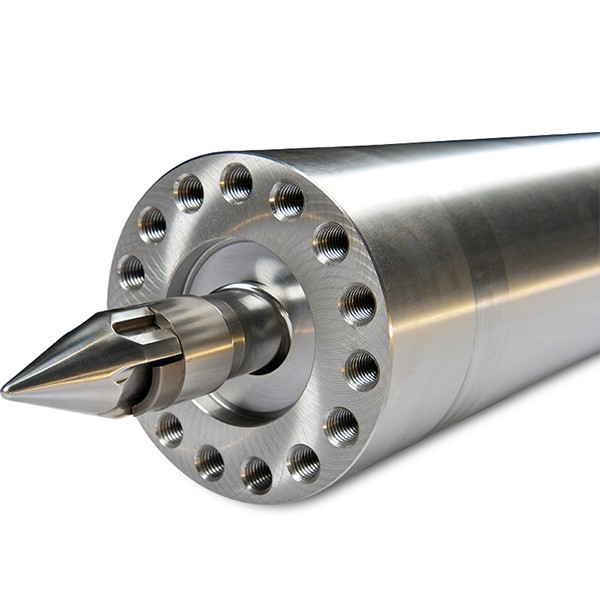
Barrier screw
A new type of barrier screw has been developed for feeding feed screw applications. Its innovative structure eliminates the drawbacks of conventional barriers and provides superior performance. Its novel design minimizes the formation of dead-spots and terminates at shallow channel depths. It also ensures that the screw conveys melt in an adequate volume, without excessively reducing or increasing the width of the channel.
The screw is generally made of two components: a metering section and a compression section. The metering section is made up of a helical main flight and is designed to maintain a substantially constant lead in the feeding section. The two parts are interlocked by a helical feed channel.
Tapered root
The Tapered Root Feed Screw is a widely used industrial screw. It is standardized in geometry and nomenclature. Its performance has been proven in various fields. Its advantages over other similar screws include reduced energy consumption, high productivity and easy maintenance. It is the most popular type of screw in the industry.
The tapered shank screw's pointed end allows it to be driven directly into a material. Its non-tapered counterparts cannot be used in this way. In fact, the point of a non-tapered screw is narrower as it approaches the head.
Parallel root
The length to diameter ratio (L/D) of feed screw is the ratio of the effective part length and screw outer circle. For instance, the conical twin screw has large end diameters and small end diameters. Thus, the L/D ratio is the average of these two values. A parallel root of feed screw is a screw with a pitch between 0.5 and 2.3240.
Alloy steel
The process of coating an Alloy steel feed screw involves heating the alloy and then cooling it in a controlled manner. This process creates a dense, crack-free coating on the screw. During the process, the feed screw is heated to a specific temperature to fuse the alloy to the substrate.
The alloy coating process starts by heating the feed screw to a temperature of 250 to 300 degrees F. The feed screw is cleaned and grit-blasted prior to the application of the coating. The feed screw is then sprayed with the alloy at a minimum particle velocity of 2,400 ft/sec. The screw is then allowed to soak at this temperature for one to six hours.
Polyethylene
Choosing the right polyethylene feed screw can make a big difference in the performance of your manufacturing process. The right feed screw material will help you match the characteristics of your plastic to the needs of your specific application. This will improve its durability and function, minimize problems and ensure the best possible final part product. Here are a few tips to help you find the perfect material for your feed screw.
Choosing a feed screw with the right design is essential to ensure that your polymer pellets are melted evenly. The right feed screw design will help you avoid waste, allowing your company to maximize production.
Vented barrel
A Vented barrel feed screw is a screw that has two distinct stages. The first stage is a feed zone with constant depth, while the second is a transition and metering zone. This design allows for the release of volatiles without vent bleed. In this case, the depth of the feed zone is shallower than the metering zone, allowing for more even mixing.
This type of screw has an eccentric root configuration. Its design creates a circulation pattern in the gap. Its design allows for water cooling throughout its length and also improves the mixing in the final flights. Alternatively, some screw designs incorporate a central passage that prevents the screw from sticking to the root in the feed zone.